Features of RedoxMaster®
RedoxMaster® technology is a revolutionary drying technology developed by Glencal Technology Co., Ltd. It is a completely new and unconventional drying technology that dries organic materials at an overwhelmingly low cost (approximately one third to one twentieth) compared to conventional technologies, while significantly reducing carbon dioxide emissions (approximately 40% to 80% less CO2 emissions), at low temperatures (20°C to less than 100°C) and quickly (several hours to one day) without carbonising or oxidizing them.
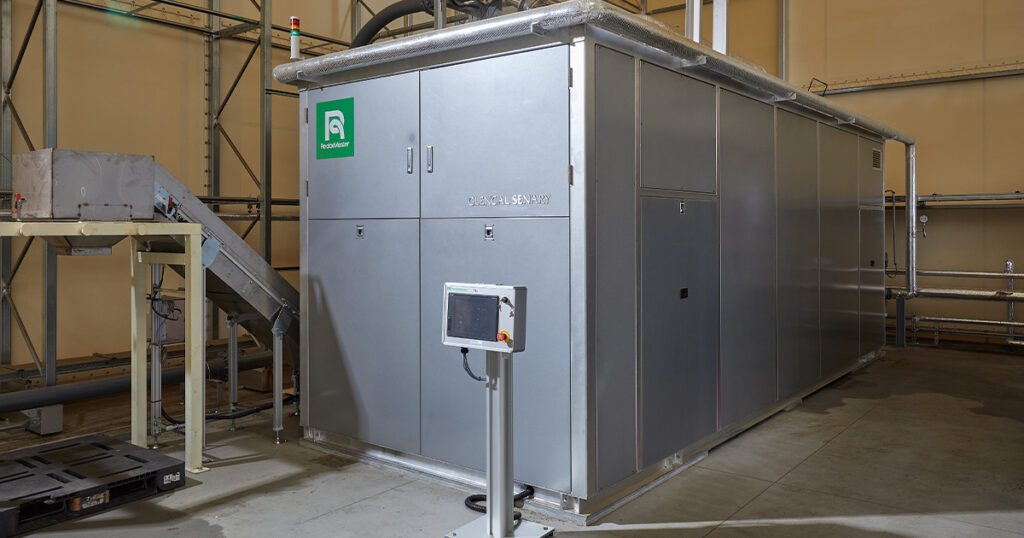
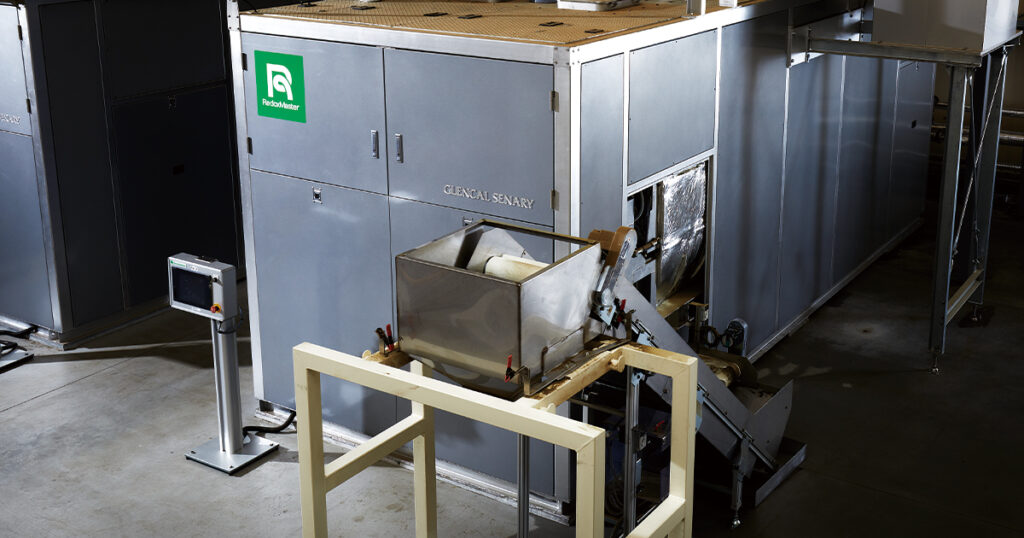
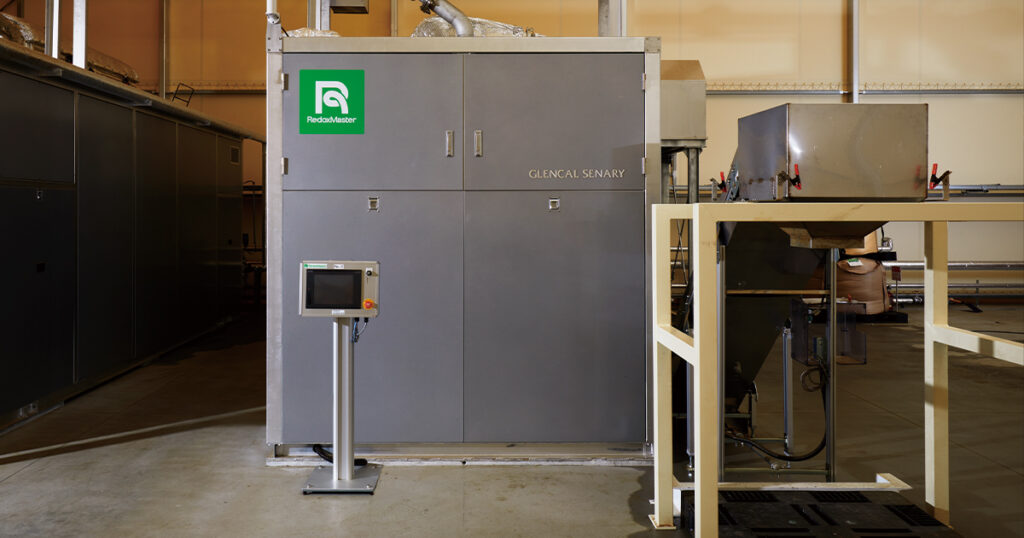
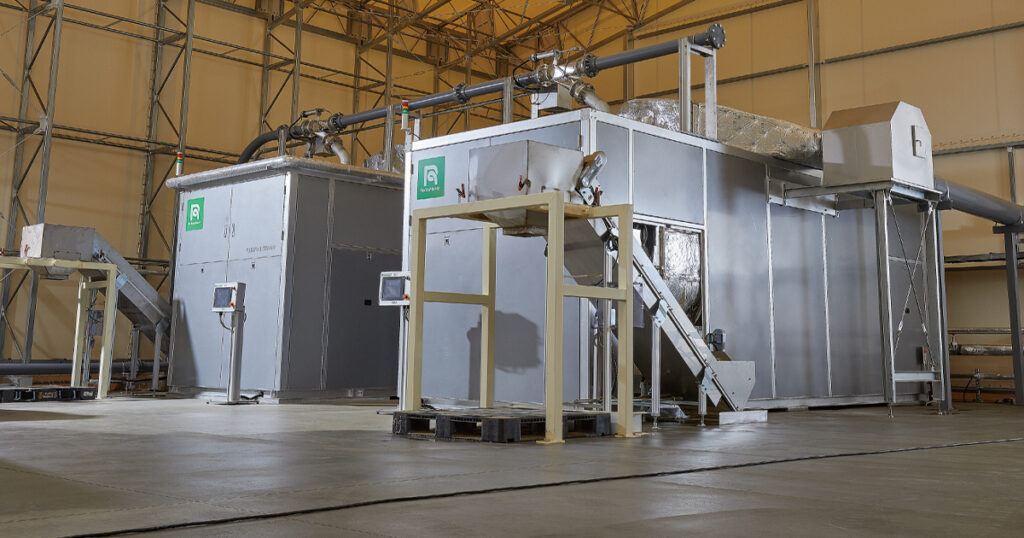
Dries organic materials quickly, at low temperatures and with low CO2 emissions.
The most outstanding feature of the RedoxMaster® is that it can dry organic materials such as coffee bean pomace, apple pomace and pruning waste to a moisture content of less than 12.5%, which is suitable for long-term storage, at a very high speed without carbonisation or oxidation, which is almost impossible with conventional high-temperature drying technology.
Conventional centrifuge drying system can dry only to a moisture content of up to 85%. Decompression (vacuum) dryers can also achieve results close to those of the RedoxMaster® in terms of moisture content, but the condition of the treated material is often dumpling-like and it is difficult to prevent oxidation and carbonisation completely, making it difficult to use as a material for bioplastics, feed, fertiliser and fuel. In addition, the installation and running costs of these systems are extremely high, making their introduction into the market difficult in many cases, and they also emit large amounts of carbon dioxide, which is a significantly problematic from the viewpoint of ESG management.
Compared with these conventional technologies, RedoxMaster® can dry to approximately 3% moisture content in 8 to 24 hours in the most efficient cases, depending on the type of the material, and achieve a volume reduction of roughly 90% up to 99% on a weight basis.
Overwhelmingly low running costs compared to conventional technologies
It is possible to reduce the moisture content of organic materials to 50% to 20% or less by using decompression (vacuum) drying equipment, which is considered the most advanced of the existing technologies. However, decompression drying equipment requires the creation of a vacuum, consequently the initial investment cost of the facilities is enormous. Moreover, they consume large quantities of fuel and electricity, and the running costs are very high. It also emits large amounts of carbon dioxide. Drying methods using conventional techniques is extremely costly and has a high environmental impact.
The amount of heat required to boil and evaporate 1 g of water at a water temperature of 25 °C is approximately 2.5 kilojoules. In addition, about 2.28 kilojoules of energy is required to evaporate 1 g of water at a water temperature of 25 °C at 25 °C . On the other hand, when tested using the RedoxMaster®’s drying engine, the amount of energy required to evaporate 1g of moisture at an article temperature (water temperature) of 25°C under optimum operating conditions was approximately 17 joules. This means that in bench tests, the energy consumption is less than 1/100 of that of conventional technologies.
In actual operation of the RedoxMaster® machine, the results will not be the same as in bench tests, as additional electricity is required to drive the motors, blowers, etc. used to run the equipment, but the results will still be between one third and one twentieth of those achieved with conventional technologies. CO2 emissions can be reduced by 40% to 80%, while running costs can be reduced by 30% to over 90% to dry the target material. (*CO2 emissions and running costs increase or decrease depending on the moisture content of the target after treatment, as well as the nature and properties of the treated organic material.)
Nearly no effluent or emissions breaching environmental regulations
RedoxMaster® technology is an innovative technology that promotes water evaporation at low temperatures, from approximately 20°C to less than 100°C, without the use of high heat. Therefore, unlike conventional high-heat drying technologies, it can dry the objects to be treated without carbonising or oxidising them. This feature generates significant added value.
For example, in the drying treatment of strained lees of coffee beans, apple juice, green tea, the moisture content can be reduced to below 12.5%, a level at which rotting does not proceed, while minimising damage to polyphenols, fibre and other valuable components in the wastes. Food residues treated with RedoxMaster® retain these valuable ingredients and are easily stored and transported over a long period of time. As a consequence, the waste can be utilised as a high-quality raw material for animal feed, supplements, fertilisers and food. RedoxMaster® does not only reduce drying treatment costs, but also utillise the treated residues as high-value-added by-products.
Another significant difference from conventional drying methods is that the residues treated by conventional dryers often harden into clusters like dumpling, whereas residues treated by the RedoxMaster® become extremely fine and uniform particles, making them easy to use as raw materials for biomass plastics, animal feed, fertilisers, fuels, etc. The low-temperature drying technology of RedoxMaster® is the key of making high-quality by-products.
RedoxMaster® does not emit any harmful exhaust (scrutiny by third-party inspectors has been carried out) and does not discharge polluted water into rivers or groundwater. While effluent standards are becoming stricter at home and abroad, RedoxMaster® emits no effluent, so there is no need to install a drainage system, and therefore no need to care for effluent regulations and the cost of installing a large drainage system.
The machines specialising in reducing liquid waste are capable of condensing between 5 and 20 tonnes per day of liquid and near-liquid waste (moisture content》90%). For example, by using this machine, digestate generated from biomass gas plants can be concentrated to a moisture content of 70~80%, and its weight can be reduced by 70% approximately. (The digested liquid after the treatment is used as concentrated liquid fertiliser). The machine is also being demonstrated for use as a small-scale high-performance sewage treatment unit and for application in food processing. (*Throughput and treatment rates would change depending on various conditions, such as the type of residues, ambient temperature and humidity.)
The drying process of the RedoxMaster® produces virtually no odour. Therefore, even if RedoxMaster® is installed onsite at a food factory, the surrounding environment will not be worsened by odour. (* Odours from the organic waste itself can be lessened by optional deodorising equipment, if necessary. In most cases, these facilities are not necessary.)
Domain of RedoxMaster®
we are developing our business in eight major segments.
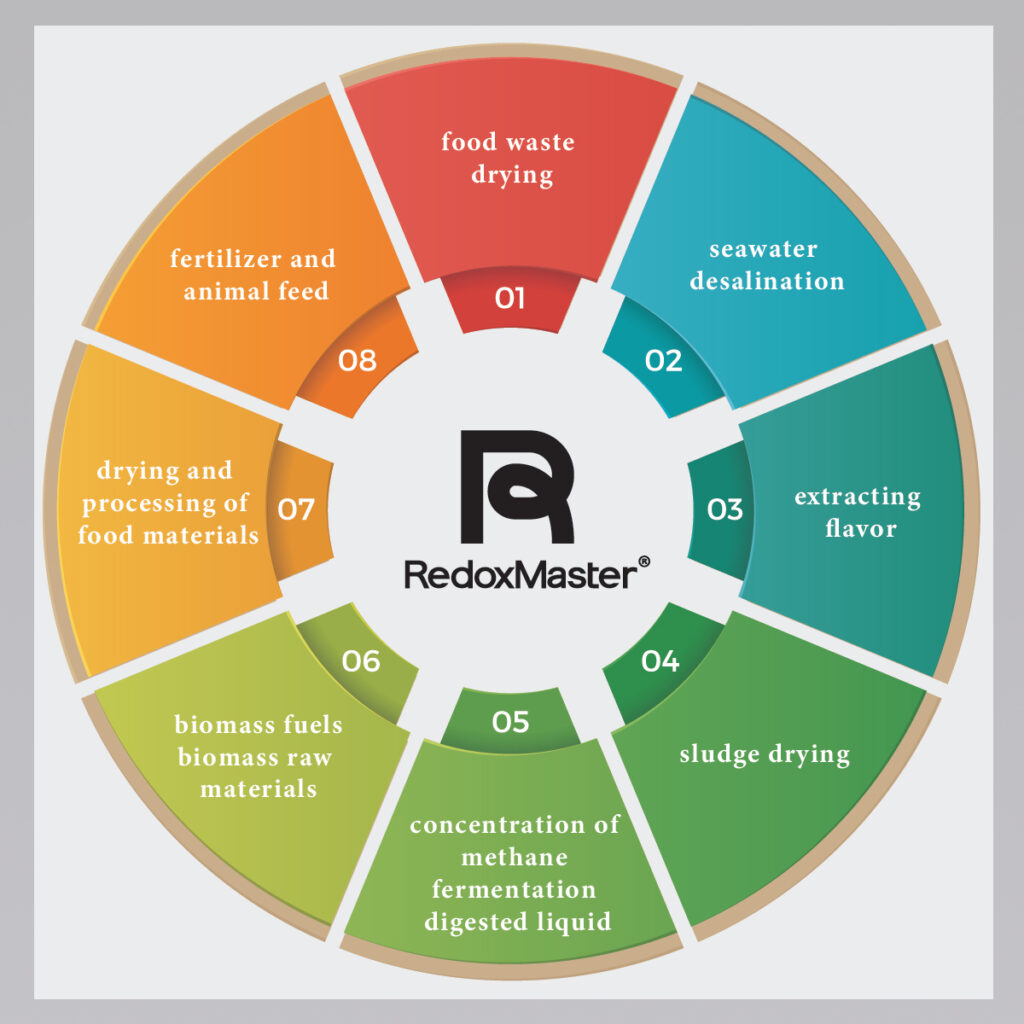
Representative successful examples of organic wastes
「Apple juice pomace, orange pomace, carrot pomace, cabbage residue, onion residue, coffee bean residue, green tea residue」「Digestate from biomass power plants」「Prunings, grasses and trees」「Seaweed stalks」「Sea squirt shells」「Chinese herb medicine materials」「Curry roux, stew roux etc.」「Raw fish waste」「Sake residues from the production of sake.「Livestock faeces (urine)」「Animal meat such as beef, chicken, pork, etc.」「Sewage sludge」
Specifications
international patent:(JP)7072791、(JP)6712419、(JP)6703671、(US)16/965,598、(AUS)2019210824、(NZ)766809、(JP)7098176
trademark registration:(JP)5979168、(JP)5979169、(EU)018574142、(UK)UK00003708705、(AUS)2222365、(NZ)1193116、(IND)5196824、(UAE)370034、(UAE)370036、(JP)6274917、(JP)6274918、(JP)6274919、(JP)6434270、(EU)018573652、(UK)UK00003708706、(AUS)2222366、(NZ)1193121、(UAE)370037、(UAE)370039、(UAE)370040、(JP)6440702、(JP)6567416
Model | RM30 |
---|---|
Standard processing ability | 1~7 m3/day |
Power source | 3 phase 200V 50/60Hz |
Electricity consumption | 41kw/hour(rated) |
Volume reduction rate | 50~90%/day |
Size Volume | (LWH):9,410㎜×2,490㎜×2,640㎜ appx 13,500KG |